На заводе двигателей «КАМАЗа» модернизировали мойки для деталей
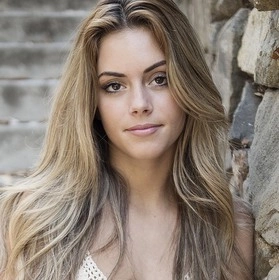
- 05 декабря 2021 19:38
- Аня Суслова
Чистота детали — важный параметр, без которого на производстве не обойтись. От него напрямую зависит качество выпускаемой продукции. Ведь как собирать, к примеру, двигатель, если на масляную неочищенную деталь налипли пыль и грязь? На заводе двигателей об этом знают не понаслышке и о «гигиене» деталей позаботились: в цехах 201 и 113 провели масштабную модернизацию комплекса трех моек, — пишут «Вести КАМАЗа».
Необходимость в этом назревала давно: по словам начальника центральной заводской лаборатории технологической точности ЗД Владимира Борисова, старые версии моек работали больше 40 лет каждая. И возраст дал о себе знать: прохудились баки, плохо работали форсунки, подающие воду, нагревательные элементы не давали нужной температуры, а транспортная система износилась и подверглась коррозии.
А без моек не обойтись, ведь детали, которые нужно качественно отмыть, важные — например, это кольцо газового стыка, коромысло клапана и шестерни коробки передач. Прежде при простое приходилось изготовленные детали переносить, а габаритные — перевозить на находящиеся поблизости мойки, а ведь лишнего времени на производстве не бывает. Более того, не каждая деталь подходит к определенной мойке: бывало, детали не влезали или, напротив, проваливались в ячейки транспорта.
Задачу перед исполнителями главный инженер завода поставил серьезную — модернизировать пришлось буквально все.
— Корпус новых моек изготовили из нержавеющей стали — больше никакой ржавчины, да и срок эксплуатации увеличивается, — рассказывает Борисов. — Все приводные валы и детали узлов сделаны из нержавеющей стали или с гальванопокрытием, приборы контролируют и уровень заливки воды и моющего раствора в мойку, и температуру. Цикл обработки теперь составляет две минуты, раньше мойка занимала больше трех минут.
Поменялась и конструкция моек — под каждый вид детали сделали свою систему и одновременно максимально ее упростили. Закупили новые транспортные сети, которые рассчитаны по размеру ячеек на конкретную составную часть будущего двигателя: больше никаких проблем с мелкими деталями, которые в прежнем варианте моек могли провалиться или застрять. Проработали систему промывки, продувки и сушки — на выходе получается чистая, обработанная (в моечном растворе содержатся антикоррозийные компоненты) и полностью сухая деталь.
Работа проделана колоссальная. И все это с минимальными затратами!
— На одну мойку потребовалось порядка 100 тыс. рублей. Часть комплектующих делали на нашем же заводе, — говорит Борисов. — Экономический эффект от модернизации, по нашим расчетам, составит около трех миллионов рублей в год на одну мойку.
Модернизация на этом не закончена: по словам Борисова, до конца текущего года планируется автоматизировать процесс загрузки деталей в моющие машины. Уже продумали и составили схему транспортного агрегата, который будет забирать компоненты и отправлять их «в душ». Это позволит сократить время обработки деталей и снизить потери на транспортировку.
- Телеграм
- Дзен
- Подписывайтесь на наши каналы и первыми узнавайте о главных новостях и важнейших событиях дня.
Войти через социальные сети: