На ПРЗ начался монтаж оборудования для производства рам КАМАЗов от К3 до К5
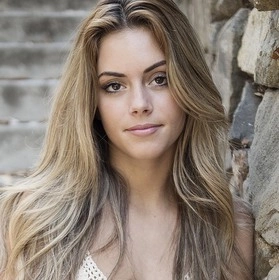
- 03 июля 2020 17:08
- Аня Суслова
На прессово-рамном заводе начался монтаж оборудования для нового производства рам с высокими прочностными характеристиками семейств грузовиков КАМАЗ от К3 до К5. Общая площадь работ составляет около 15 тысяч квадратных метров., пишут «Вести КАМАЗа».
Подготовку к финальному этапу проекта начали заранее. Площадка была освобождена от оборудования, для размещения новых линий смонтированы фундаменты, сделаны наливные полы. Сейчас ведётся расстановка будущих агрегатов, разметка полов. Конвейер сборки рам будут собирать специалисты фирмы «Инжер», линию окраски — изготовитель, линию профилирования лонжеронов — прессоворамщики.
По проекту изготовление рамы начнётся с профилирования лонжеронов. На автоматической линии рулон высокопрочной стали будет кроиться на профили разной толщины и длины — в зависимости от модели большегруза. Следующий агрегат будет делать перфорацию в соответствии с техническим заданием.
Параллельно будет расположена линия окраски.- Сейчас на ПРЗ неокрашенный лонжерон сразу отправляется на сборочный конвейер. Рама окрашивается в сборе, а на изделия со специальными требованиями к толщине покрытия и рамы перспективного семейства накладывается ещё один слой эмали, — вводит в курс дела начальник отдела реинжиниринга ПРЗ Ильнар Сатдаров. — Но при таком подходе риск коррозии всё равно остаётся. Существенно снизить его позволит окраска всех элементов перед соединением. Новая технология включает в себя обезжиривание (мойку), дробемётную обработку, подготовку поверхности изделия, катафорезное грунтование, электростатическое напыление порошка и финальную операцию — контроль качества и исправление дефектов. Комплексная толщина покрытия будет не менее 80 микрон.
Основные сложности процесса — агрегаты внушительных размеров (объём ванн для грунтования — 70 кубометров) и точность, с которой необходимо смонтировать высокотехнологичное оборудование. После окраски лонжероны будут подаваться на склад, а оттуда доставляться на первую позицию сборки рам.
На новом конвейере сборки рам предусмотрены встроенные элементы обеспечения качества, значительно облегчающие процесс изготовления. Это лазерная разметка контуров деталей на лонжероне; выделение при заезде рамы на позицию сборки световым индикатором деталей, которые необходимо установить на раму; гайковёрты с обратной связью для крепления резьбовых соединений.
Логистика производства будет полностью автоматизирована. Она включает в себя перемещение деталей на участке завески, транспортировку к линии окраски, автоматическую перевеску на окрасочную траверсу иобратно, размещение деталей на автоматизированном складе и подачу их на позицию сборки.
При проектировании линии был применён принцип end-to-end — сквозная работа без лишнего перекладывания, с автоматической подачей данных по актуальному статусу деталей, которые находятся на складе и на позициях сборки. Это исключит необходимость ручного подсчёта номенклатуры.
Производство рам рассчитано на выпуск 65 тысяч изделий. Их качество будет гораздо выше, а коррозийная стойкость вырастет в три раза — до 1500 часов в соляном тумане. Запуск нового производства намечен на первую половину 2021 года.
- Телеграм
- Дзен
- Подписывайтесь на наши каналы и первыми узнавайте о главных новостях и важнейших событиях дня.
Войти через социальные сети: