Как казахстанский проект поможет челнинской «литейке»
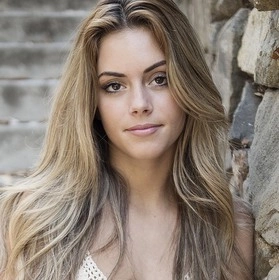
- 11 февраля 2021 15:44
- Аня Суслова
Как казахстанский проект поможет челнинской «литейке»? Сколько литья камазовский завод поставляет на свободный рынок? В интервью «Вестям КАМАЗа» директор ЛЗ Эдуард Панфилов рассказал о перспективах модернизации нескольких производственных площадок и описал стратегию развития «литейки» в целом.
1,3 МИЛЛИАРДА ВЫРУЧКИ ТОЛЬКО НА СВОБОДНОМ РЫНКЕ
— Эдуард Владимирович, расскажите, пожалуйста, что представляет собой литейный завод «КАМАЗа» — какова его производственная структура, ведущие направления деятельности?
— Наш завод — это комплекс производств, который при постройке в 1970-х годах вобрал в себя лучшие мировые практики и впоследствии постепенно модернизировался. Прообразом производства чугунного литья, к примеру, стал один из заводов Ford. Основные наши площадки — это корпуса чугунного литья, стального литья, цветных сплавов — алюминиевых, медных, бронзовых, латунных и даже цинковых. Еще в одном корпусе располагается цех точного стального литья, практически не требующего обработки, а также цех поршневых колец и производство литейной оснастки, какого на территории России, я полагаю, ни у кого больше не осталось. Мы полностью обеспечиваем себя оснасткой и одно время даже торговали ею на свободном рынке. Общая площадь литейного завода — порядка 222,6 гектаров, на которых размещены и другие промышленные участки, и многочисленные службы. Инжиниринговая сеть завода закрывает все потребности сложных производств. У нас, к примеру, есть компрессорные станции для производства сжатого воздуха, градирни для охлаждения воды, мощные системы вентиляции и фильтрации, развитая сеть складов с двумя железнодорожными ветками, два независимых источника электроэнергии… Сложно найти инженерное направление, не представленное на заводе.
— Учитывая, что сырье вам приходит через центр закупок «КАМАЗа», ваши поставки на смежные заводы, видимо, тоже не подразумевают денежных расчетов? Иначе говоря, корректно ли говорить о выручке «литейки»?
— Выручку имеет смысл рассматривать в контексте всего «КАМАЗа», но для понимания скажу, что в 2020 году литейный завод исполнил бизнес-план по объемам производства и увеличил маржинальный доход на 17 процентов в сравнении с 2019 годом. В наступившем году нам будет посложнее — задачи ставятся серьезнее.
— Какова доля продукции диверсификации на литейном заводе — той, что идет на свободный рынок?
— До 2020-го года она занимала около 30 процентов всего объема производства. За месяц мы продавали в среднем на 100−150 миллионов рублей, за год выходило примерно 1,2−1,3 миллиарда. В прошлом году рынок упал по понятным причинам, но это временный спад.
«ТАКТИЧЕСКАЯ ЗАДАЧА ПО КАЗАХСТАНУ — РАЗГРУЗИТЬ НОМЕНКЛАТУРУ ЧЕЛНИНСКОГО ЗАВОДА»
— Насколько реальная среднегодовая загрузка соответствует проектной мощности завода?
— Говоря о мощности, нужно иметь в виду объем номенклатуры. Проект завода предусматривал производство лишь трех моделей КАМАЗов — 5511, 4310 и 53205, которая добавилась со временем. Перечень чугунной номенклатуры для них включал 96 позиций при колоссальных объемах производства, 411 тысяч тонн в год. Сейчас мы выпускаем порядка 500 позиций, включая мелкую серию, плюс единичные заказы — еще около 150 наименований. Плюс работаем со сплавами: сейчас в производстве чугунного литья используется шесть различных сплавов, а по проекту их было всего два. С такой сумасшедшей номенклатурой очевидно, что заложенные при строительстве параметры в современных реалиях следует пересчитывать с определенным коэффициентом. До проектной планки мы не дотягивали никогда — рекордной цифрой, если не ошибаюсь, были 298 тысяч тонн. В 2020-м году выпустили 130−140 тысяч тонн по всем подразделениям. Полагаю, если просто модернизировать завод, ничего не достраивая, можно выйти на загрузку 40−45 процентов от проекта, но грузовик от этого все равно не подешевеет. Поэтому стратегией «КАМАЗа» остается разделение производства по серийности номенклатуры: единичную нужно выпускать в одном месте, сложные отливки — в другом, а среднесерийную оставить здесь, на челнинском литейном заводе. Таким путем мы выйдем на европейскую ценовую политику, и загрузка производства тоже возрастет. Это ведь замкнутая цепочка: чем дешевле литье — тем дешевле автомобиль, отсюда выше спрос и, соответственно, потребность в литье.
— Разделение номенклатуры по серийности, наверное, подразумевает и программу реинжиниринга в Челнах, и новый литейный завод «КАМАЗа» в Казахстане. Уровень инвестиций в Костанае примерно понятен, а во что обойдется компании модернизация основной «литейки»?
— Суммы непубличны, но могу сказать, что в Челнах на первом этапе модернизироваться будет только чугунное производство, и оно входит в общий с казахстанским гринфилдом инвестиционный план (англ. Greenfield, «зеленое поле» — строительство объекта с нуля — прим. ред). Тактическая задача по Казахстану — наладить выпуск сложных отливок в ближайшие три года и разгрузить номенклатуру челнинского завода, чтобы мы могли отказаться от разносорта. Передовой завод с элементами ноу-хау сможет выпускать в Казахстане продукцию лучшего качества с меньшей ценой.
— Каким вы видите будущее челнинской площадки в свете этого проекта?
— Мы продолжим выпускать тонны продукции, необходимой для сборки автомобилей всего модельного ряда. Объем производства не пострадает, рабочие места сохранятся. Когда казахстанский завод позволит нам сконцентрироваться на изделиях большей серийности, мы значительно сократим финансовые издержки, время и трудозатраты на перенастройку оборудования. Мелкая серия, которая останется в Челнах, будет отдана на аутсорсинг, и мы активно ищем партнеров. Около 70 мелкосерийных отливок уже размещены на Тутаевском моторном заводе. Есть и другие подходящие предприятия в России, с которыми мы договариваемся, помогаем в освоении наших позиций с точки зрения качества. Не стоит забывать, что камазовское литейное производство все-таки остается ведущим в стране. У нас и научный потенциал довольно высок: персонал защищает кандидатские диссертации, публикуется в престижных специализированных журналах вроде «Литейщика России».
«БУДЕТ ОБНОВЛЕН БОЛЬШОЙ ПЕРЕЧЕНЬ ОБОРУДОВАНИЯ»
— Насколько масштабная модернизация ждет чугунное производство?
— Будет обновлен довольно большой перечень оборудования. Мы уже закупили три 65-тонные индукционные печи выдержки с полезным объемом 50 тонн. Первая уже монтируется, еще две поступят на завод в течение года. Печи — наиболее энергоемкое оборудование, поэтому мы с них и начали. Кроме энергопотребления, скорости плавки и других важных потребительских свойств они отличаются и отсутствием шума. Их шумовой уровень равен 20−30 дБ, что примерно соответствует акустическому фону обычной комнаты. Дыма тоже выделяется в несколько раз меньше, что важно с точки зрения условий труда. В будущем мы планируем модернизировать две формовочные линии совместно с изготовителем оборудования — фирмой HWS. Запчасти уже закуплены, но пока мы ждем возможности для приостановки технологических процессов, чтобы смонтировать линию.
— Производство литейной оснастки потребует обновления?
— Оно уже неплохо укомплектовано, но, вероятно, мы докупим несколько установок для цифровизации разметки отливок. Одна такая машина у нас есть — она сканирует поверхность, создает облако точек, которое накладывается на трехмерный конструкторский чертеж и мгновенно выявляет отклонения. Скорость разметки повышается в разы. Думаем купить еще 3−4 такие машины, по одной на каждое производство. По конструкторским и технологическим направлениям рассматриваем закупку новейшей версии программы Magma, которая моделирует заливку и кристаллизацию, и даже может давать прогнозы на основе мировой базы технологий. Тест программы показал отличные результаты: она выведет нас на новый уровень проектирования технологий, повысит и стабильность, и скорость разработок. Именно в скорости мы серьезно отстаем от европейских конкурентов.
— Имеются ли перспективные проекты вне программы реинжиниринга?
— Несколько новых проектов будут реализованы под эгидой госкорпорации Ростех. В 2021—2022 годах мы должны начать выпуск алюминиевых блоков цилиндров и головок блоков цилиндров для определенных моделей автомобилей, оборудование уже контрактуется. Когда участок цветного литья выйдет на проектные показатели по сложным отливкам, проект даст нам дополнительный оборот порядка миллиарда рублей в год. Он позволит и квалификацию персонала подтянуть, и в очередной раз подтвердить потенциал литейного завода. Да и товар, полагаю, лишним не будет. В общем, я очень рад, что Ростех доверил эту задачу «КАМАЗу», потому что выбор, насколько я понимаю, был.
«СРЕДНИЙ ВОЗРАСТ РУКОВОДЯЩЕГО СОСТАВА — 44 ГОДА, ПРИЧЕМ СО СТАЖЕМ ПО 15−25 ЛЕТ»
— В этом году литейному заводу исполняется 50 лет. В каком составе он встречает полувековой юбилей?
— Общий штат завода насчитывает 4,7 тысячи человек — это внушительная цифра в масштабах «КАМАЗа». К юбилейной дате мы подходим с серьезными достижениями в областях энергоэффективности, производительности труда, снижения дефектности. За последние 6 лет, к примеру, объем брака снизился в 2,5 раза. Я очень рад, что коллектив постоянно пополняется молодыми кадрами, и мы при этом сохраняем преемственность опыта. Сегодня средний возраст руководящего состава — мастеров, начальников цехов и производств — 44 года, причем со стажем по 15−25 лет, наработанным именно на литейном заводе «КАМАЗа».
— Как меняются условия труда для этих людей?
— В постоянном режиме. Возьмем для примера средства индивидуальной защиты. За последние 5 лет мы одних только респираторов перепробовали свыше 60 видов в поисках оптимального варианта. Защитных очков прогнали через пробную эксплуатацию 33 типа, не говоря уж о спецодежде.
— Уровень подготовки персонала растет?
— Я считаю, что служба персонала — это гордость литейного завода, потому что в условиях частичной утраты вузами образовательных компетенций мы все же находим кадры, полностью соответствующие требованиям и по профессиональным, и по личным качествам. Но это не отменяет наших планов, связанных с мощным коучингом персонала. Дополнительное обучение мастеров, начальников цехов, бригадиров, формовщиков и заливщиков уже стартовало. Оно обусловлено закупками нового оборудования и изменением технологической цепочки, но есть и альтернативное движение: мы сейчас внедряем в чугунном производстве потоковую систему. Каждый поток привязан к одной из формовочных линий и включает в себя бригады от плавки до обрубки. Таким образом, все понимают, какую именно номенклатуру дает на выходе этот поток. Никто вне потока не может повлиять на качество изделия, процент брака зависит только от квалификации команды, взаимовыручки и надежности работы оборудования. Такой подход мы опробовали в прошлом году, определенные результаты он показал. В этом году отработаются правильная организация, приемы работы, обмен информацией внутри технологического потока. Я считаю, это позволит коренным образом изменить отношение сотрудников к работе и скорректировать график — люди, за исключением дежурного персонала, смогут спокойно выполнять план за пять дней в неделю, а в субботу набираться сил дома.
- Телеграм
- Дзен
- Подписывайтесь на наши каналы и первыми узнавайте о главных новостях и важнейших событиях дня.
Войти через социальные сети: