До конца года "КАМАЗ" обучится цифровой диагностике оборудования
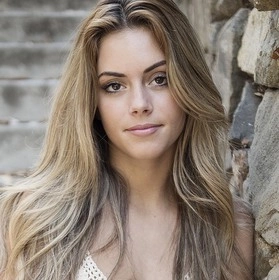
- 06 июля 2022 15:31
- Аня Суслова
Оперативная подстройка оборудования под выпуск модельного ряда К3 стала стресс-тестом для всей службы главного механика. Пришла пора искать общие пути развития для Инженерного центра и всего производства, которое обеспечивается непрерывной работой линий. Площадкой для тематической сессии стала «Фабрика процессов».
ВМЕСТО ПОКУПКИ ЗАПЧАСТЕЙ — ЦИФРОВОЙ МОНИТОРИНГ ОБОРУДОВАНИЯ
К реализации поставленных тактических задач — рестарту поколения К5, расширению линейки «Компасов» и в принципе камазовского ассортимента вместе с компетенциями — прорываться предстоит через тяжелое полугодие, в течение которого кризис острее проявит себя как в плоскости организации производства, так и в сбытовой. С таким посылом открыл сессию на «Фабрике процессов» руководитель службы стратегического планирования ПАО «КАМАЗ» Игорь Савельев, — сообщают «Вести КАМАЗа».
Директор Инженерного центра — главный механик «КАМАЗа» Айрат Галеев конкретизировал одну из важнейших проблем: основная доля оборудования на «КАМАЗе» эксплуатируется более 20 лет, а превышение срока эксплуатации автоматических линий и станков влечет за собой риск простоев, непредвиденные затраты и дополнительную нагрузку для ремонтников. В связи с чем участники сессии задумались о переходе с традиционных методов обслуживания оборудования — плановое плюс аварийное — на прогностическое, в основе которого лежит оценка текущего состояния линий и станков. В этом смысле должно помочь внедрение в Инженерном центре цифровизации обслуживания. Первый и второй этапы этого проекта позволят оперативно контролировать состояние оборудования и управлять процессом закупки комплектующих. До конца этого года оба этапа должны быть реализованы.
На «КАМАЗе» в настоящее время задействованы свыше 26 тыс. единиц оборудования, из которых 8,8 тыс. входят в основную технологическую цепочку. Наличие нового цифрового инструмента значительно смягчит положение в подразделениях, где год от года уменьшается число опытных ремонтников. Если же не предпринять никаких мер, то по прогнозу к 2025 году образуется кадровый дефицит, а к 2030-му будет утрачена часть функционала. В первую очередь это касается проведения капитальных ремонтов, которые из года в год будут дорожать. Между тем надо осваивать новые компетенции: мехатронику, преддиктивную аналитику состояния оборудования, разработку технологических процессов ремонта и технического обслуживания оборудования, ремонт электрошпинделей, робототехники, высокотехнологичного оборудования.
Кроме того, стареющему парку требуется все больше запасных частей, причем для линий со стажем они обходятся особенно дорого, поскольку серийного выпуска запчастей для них уже нет. Эта сложность накладывается на санкции, в результате которых логистические цепочки нарушены, запчасти подорожали, а сроки их поставок утратили определенность.
TPM НА ДВОЙКУ
Участники сессии попытались найти и иные решения для оптимизации простоев оборудования, обеспечения запчастями и привлечения персонала. Главным условием стала реалистичность сценариев — они должны быть исполнимы на дистанции в один-два года, а ресурсы компания найдет.
На текущий момент, по сводной оценке механиков и энергетиков, весьма слабо работает система Total Productive Maintenance (ТРМ — всеобщий уход за оборудованием) — на 2,5 балла из 10-ти. Галеев в этой связи представил проект «Рестарт TPM», нацеленный на снижение простоев. Он напомнил, что ответственность за обслуживание оборудования лежит в первую очередь на заводских операторах и наладчиках, и предложил заново отработать весь его алгоритм. Сделать это можно на пилотном участке вместе с представителями КРПС, и в случае успеха растиражировать опыт. Кроме того, необходимо создать службу заказчика ремонта, а возможно и принципиально изменить подходы к обслуживанию оборудования, если анализ подтвердит такую потребность.
Наибольшую активность аудитории обеспечила программа привлечения персонала, прямо связанная с вопросами зарплаты. Участники рассмотрели все инструменты материальной стимуляции на «КАМАЗе» — такие, как показатели KPI, совмещение должностных функций, обучение с повышением квалификации. Самым эффективным с точки зрения производственников был признан фонд стимулирования для начальников цехов: надбавки за скорость исполнения производственных задач мотивируют безотказно.
Также высоко оценили участники сессии и представленный проект, нацеленный на оперативное обеспечение производства запчастями. Авторы предложили оптимизировать аварийные закупки в рамках актуального ремонтного бюджета, а также расширить номенклатуру запчастей, изготовляемых на Ремонтно-инструментальном заводе.
- Телеграм
- Дзен
- Подписывайтесь на наши каналы и первыми узнавайте о главных новостях и важнейших событиях дня.
Войти через социальные сети: